Optimization of foil consumption in hot stamping: orthogonal printing
written May 23 2024
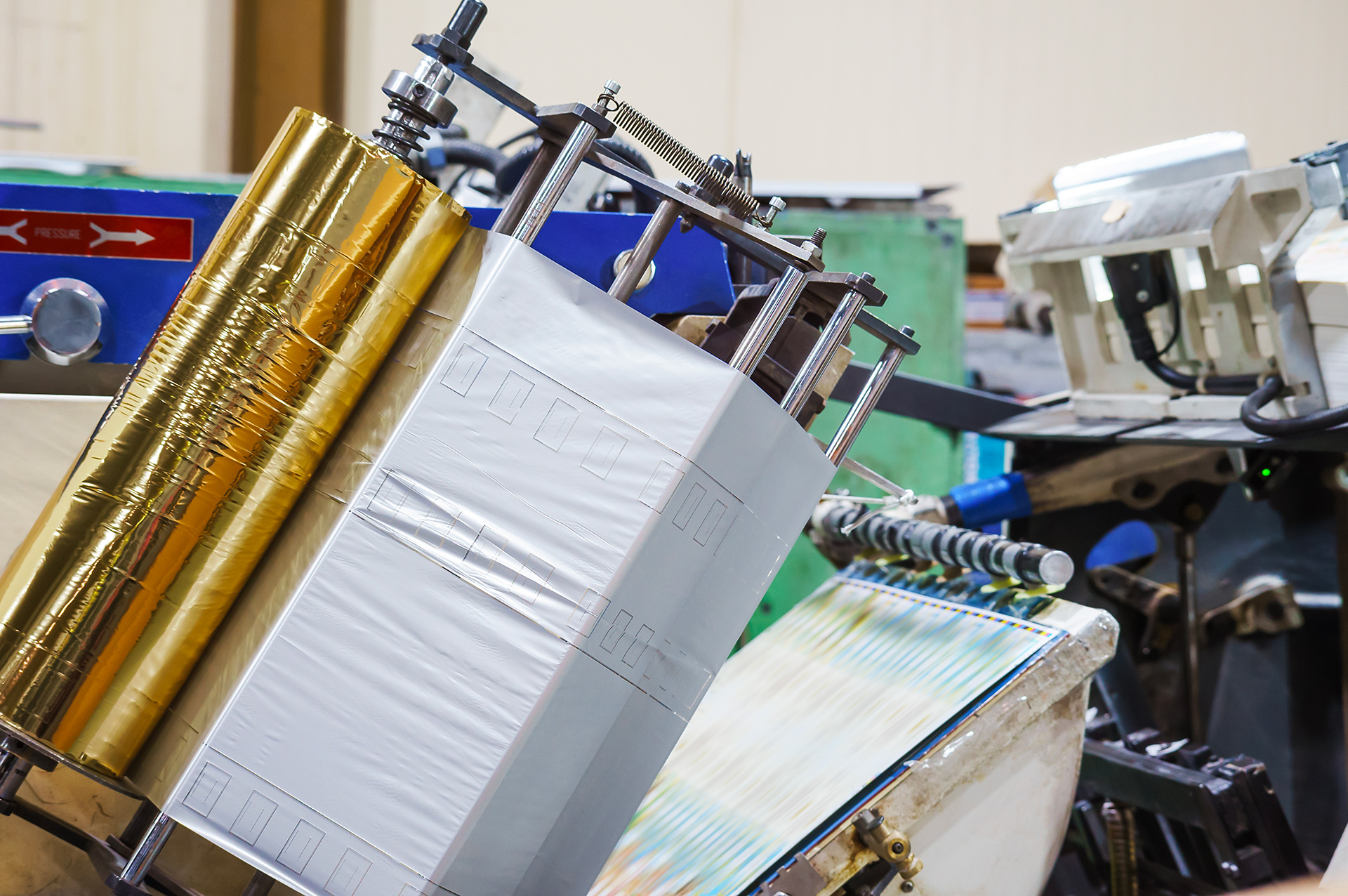
Hot foil stamping is a preparation process whereby a metal foil is transferred through a magnesium die using a rotary cylinder machine. The application of the foil occurs through a combination of pressure, heat and release speed.
Depending on the case and the mounting possibilities offered by the printing press, the foil can be mounted in the direction of the paper roll or orthogonal to it, i.e. perpendicular to the printing direction. Perpendicular mounting of the foil is possible when the foil has a lower height and width than the label surface and allows (when permitted) to reduce consumption and waste more effectively than traditional mounting.
CASE A)
We have a pitch impression and a portion of the label where the orthogonally mounted foil will be applied. In this case, if the machine allows for a different hot stamping speed, hot stamping optimization is always possible and foil consumption will be the size of the hot stamping pitch multiplied by the number of labels.
FOR EXAMPLE: We need to print 1,000 labels that have a print format (width x pitch) of 80x100 mm and a hot foil print format (width x pitch) of 50x50 mm. In this case, the paper consumption for production will be equal to the label print pitch (100 mm) times the number of labels, i.e. approximately 100 linear metres. Similarly, foil consumption will be equal to the hot foil print pitch (50 mm) times the number of labels, i.e. approximately 50 metres.
Case A: Optimizable | |
Labels to produce | 1,000 pz |
Print label pitch | 100 mm |
Hot stamping pitch | 50 mm |
Adhesive paper consumption | 100 ml |
Orthogonally printed foil consumption | 50 ml |
CASE B)
We are in the situation where we have several pitches in advance (2) and one pitch in hot foil advance orthogonal. In this case, foil optimization is possible and foil consumption is calculated by multiplying the hot foil step by the number of labels.
FOR EXAMPLE: We need to print 1,000 labels with a yield of 2 pitches in print feed and 2mm pitch spacing. Each pitch has a print size (width x pitch) of 100x60 mm and a hot foil print size (width x pitch) of 10x40 mm each. In this case, the paper consumption for production will be equal to the label print pitch (100 mm) + interspacing in the pitch for the number of labels, i.e. approximately 102 linear metres, while the foil consumption will be equal to the hot foil print pitch (50 mm) for the number of labels, i.e. approximately 50 metres.
Case B: Optimizable | |
Labels to produce | 1,000 pz |
Print label pitch | 60 mm |
Gap between labels | 2 mm |
Hot stamping pitch | 40 mm |
Adhesive paper consumption | 102 ml |
Orthogonally printed foil consumption | 50 ml |
CASE C)
We have 3 pitches with one advancing pitch and, consequently, 3 advancing pitches in the orthogonal hot foil printing direction. In this case, foil optimization is possible if the condition is verified:
Hot stamping pitch < | Pitch width |
number of pitches in hot stamping progress |
FOR EXAMPLE: We need to print 1,000 labels with a print yield of 3 pitches with 3 print runs (i.e. with one imprint in the print pitch). Each impression has a print format (width x pitch) of 60x100 mm and a hot stamping format (width x pitch) of 60x10 mm. In this case, the orthogonal hot stamping can be optimized because the hot stamping pitch (10mm) is less than the impression width (60mm) divided by the number of advancing impressions in the hot stamping pitch.
Case C: Optimizable | |
Labels to produce | 1,000 pz |
Printing label width | 60 mm |
Print label pitch | 100 mm |
Hot stamping pitch | 10 mm |
Adhesive paper consumption | 100 ml |
Orthogonally printed foil consumption | 10 ml |
CASE D)
We are in the same situation as in case C).
In this case, however, optimization of the foil is not possible as the condition is not verified:
Hot stamping pitch < | Pitch width |
number of pitches in hot stamping progress |
FOR EXAMPLE: We need to print 1,000 labels with a print yield of 3 pitches with 3 print runs (i.e. with one pitch in the print step). Each pitch has a print format (width x pitch) of 60x100 mm and a hot stamping format (width x pitch) of 80x40 mm. In this case, as the condition for the hot stamping pitch (40mm) to be less than the pitch width (60mm) divided by the number of pitches in the hot stamping advance (3) is not met, orthogonal hot stamping cannot be optimised, so the foil consumption will be the width of the label multiplied by the number of pitches, i.e. approximately 60 ml.
Case D: Not optimizable | |
Labels to produce | 1,000 pz |
Printed label width | 60 mm |
Print label pitch | 100 mm |
Hot stamping pitch | 40 mm |
Adhesive paper consumption | 100 ml |
Orthogonally printed foil consumption | 60 ml |
For simplification reasons, gaps and margins have not been taken into account.