How to calculate the hourly cost of an industrial machine
written August 17 2023
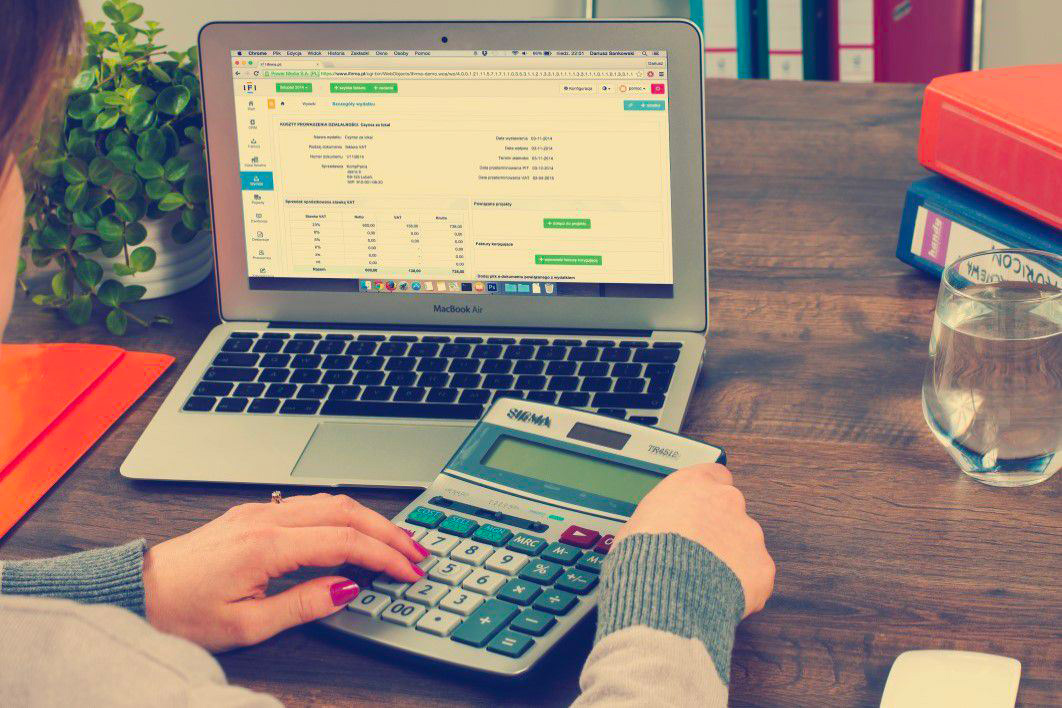
Introduction
Explaining the relevance of hourly cost calculation for industrial machinery. He emphasizes how this information is crucial for making informed decisions on production planning, production cost estimation and evaluation of operational efficiency.
Step 1: Gathering informations
First of all, collect all the necessary information. This includes:
- Purchase cost: how much did you pay for the machinery?
- Service life: how many years or hours of operation is the machine expected to last?
- Maintenance cost: estimates annual maintenance cost, including repairs, parts replacement and preventive maintenance.
- Power consumption: estimates the energy consumption of the machinery and the cost per unit of energy.
- Staff costs: determines whether staff is needed to operate the machinery, consider the salary and benefit costs.
- Capital cost: determines whether you have obtained a loan or have to pay interest on the capital invested in the machinery, consider these costs.
Step 2: Calculate the total cost
Calculate the total cost of owning and using the machinery during its estimated life cycle. This includes the initial purchase cost, maintenance cost, energy cost, staff cost and capital cost. Usually, the formula can be expressed as:
Total cost = Purchase cost + (Maintenance cost + Energy cost + Staff cost + Capital cost) * Number of years or hours of use
Step 3: Calculate the hourly cost
Once you have calculated the total cost, you can calculate the cost per hour. This helps you to understand how much it costs to operate the machine per hour of operation. The formula is the following:
Hourly cost = Total cost / Total number of hours of employment
Step 4: Consideration of planning
Now that you have calculated the cost per hour, consider how you can plan the utilization of the machinery according to this cost. For example, you could decide whether to use it in long or short shifts, based on energy rates and staff costs.
Step 5: Control and update
Costs and circumstances may change over time. Control the cost per hour regularly and update the data when necessary. This will help you keep your analysis accurate and up-to-date.
Conclusion
Highlight the relevance of calculating and monitoring the hourly cost of industrial machinery for efficient management and making informed decisions.
Important notice: this guide only offers a general overview of this process. Be sure to customize the formulas and information to the specific needs of your company and industrial machinery.
Example
Data:
- Purchase cost of the machinery: 100,000 euro
- Estimated life span: 5 years (8,760 hours per year)
- Yearly maintenance cost: 5,000 euro
- Power consumption: 10 kW
- Electricity cost: 0.15 euro/kWh
- Staff: 1 operator with an annual salary of 30,000 euro
- Capital cost: 6% annual interest
- Annual operating hours: 2,000 hours
Step 1: Calculate the annual costs
- Maintenance cost: 5,000 euro/year
- Power cost: 10 kW * 0.15 euro/kWh = 1.50 euro/hour
- Staff cost: 30,000 euro/year
- Capital cost: (100,000 euro * 0.06) / 5 years = 12,000 euro/year
Total annual costs = Maintenance cost + Power cost + Staff cost + Capital cost
Total yearly costs = 5,000 + 1.50 * 2,000 + 30,000 + 12,000 = 58,000 euro/year
Step 2: Calculation of total cost over 5 years
Total cost = Purchase cost + Total annual costs * Number of years. Total cost = 100,000 + 58,000 * 5 = 390,000 euro
Step 3: Calculate the hourly cost
Total number of operating hours = Number of years * Annual operating hours. Total number of operating hours = 5 * 2,000 = 10,000 hours
Hourly cost = Total cost / Total number of hours of use hourly cost = 390,000 / 10,000 = 39 euro/hour