Evaluating Company Inventory (Batch evaluation vs FIFO vs LIFO vs Weighted Average Cost)
written February 07 2023
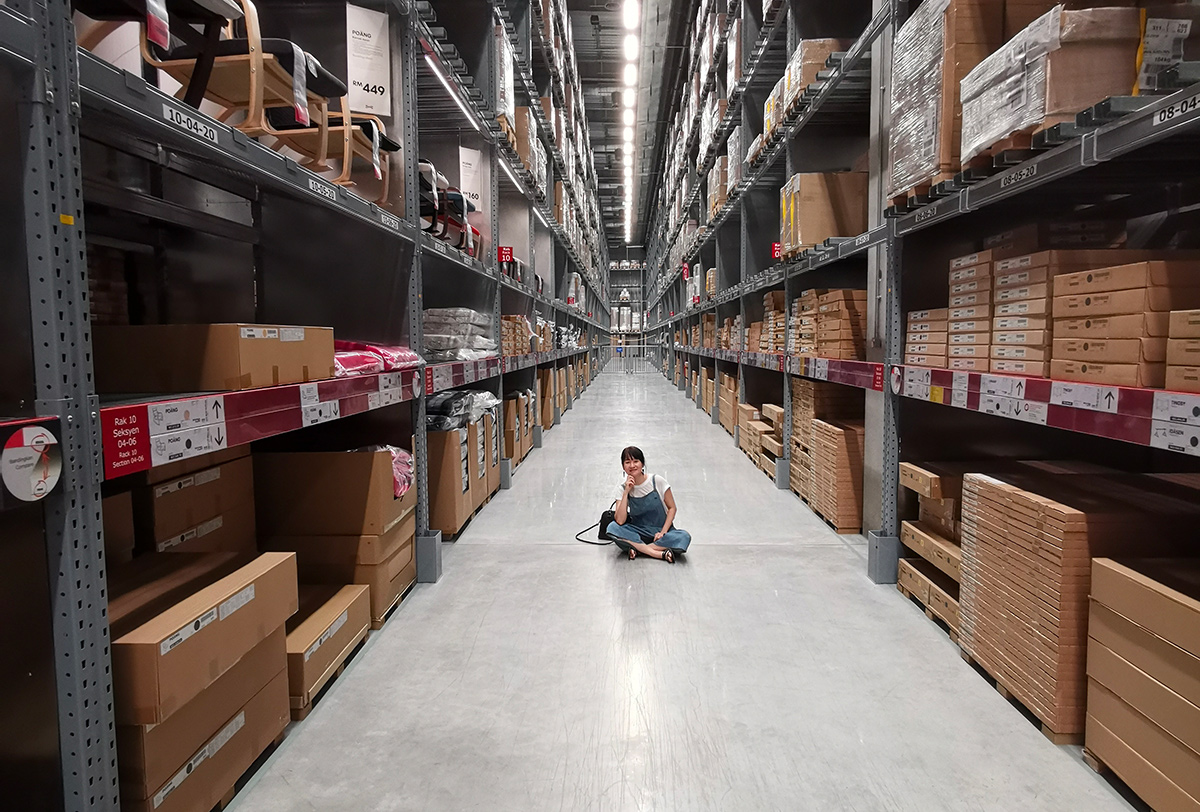
Inventory is a critical component of a business and its value can greatly impact a company's financial statements. Therefore, it is important to have an accurate and reliable method of calculating the value of inventory. Here are some of the most commonly used methods for calculating the value of inventory:
First-In, First-Out (FIFO): This method assumes that the first items purchased are the first items sold. Under this method, the cost of the most recent purchases is used to value the remaining inventory.
Last-In, First-Out (LIFO): This method assumes that the last items purchased are the first items sold. Under this method, the cost of the oldest purchases is used to value the remaining inventory.
Weighted Average Cost: This method calculates the average cost of all items in the inventory and applies it to all units in stock. This method takes into account the cost of all items in the inventory and not just the most recent or oldest purchases.
Specific Identification: This method values inventory based on the actual cost of the specific items in stock. This method is typically used for unique or high-value items that are easily distinguishable from other items in the inventory.
Retail Method: This method values inventory based on the estimated cost to replace each item in the inventory and the estimated selling price. This method is typically used by retailers to value their inventory.
It's important to note that different methods may produce different results and the choice of method depends on various factors such as the type of inventory, the purpose of the valuation, and accounting requirements. Companies should carefully consider their inventory and choose the method that best suits their needs.
Specific identification is a method of inventory valuation that values each item in the inventory based on its individual cost. This method is typically used for unique or high-value items that are easily distinguishable from other items in the inventory.
Batch identification is a variation of the specific identification method. Under batch identification, items are grouped into batches based on similar characteristics such as product type, manufacturing date, or location. The cost of each batch is then used to value the items within that batch. This method is useful when there is a high degree of variability in the cost of individual items within a product line.
For example, a manufacturer of custom-made jewelry might use batch identification to value its inventory. The manufacturer could group the jewelry into batches based on the type of metal used and the cost of the metal at the time of manufacture. The cost of each batch would then be used to value the items within that batch.
Batch identification is more complex than other methods of inventory valuation, but it can provide a more accurate representation of the cost of the inventory. It is important to have a system in place to track the batches and their associated costs to ensure the accuracy of the inventory valuation.
In conclusion, specific identification with batch identification is a method of inventory valuation that values each item in the inventory based on its individual cost or the cost of the batch to which it belongs. This method is useful when there is a high degree of variability in the cost of individual items within a product line and provides a more accurate representation of the cost of the inventory.