Industry 4.0 - 5 reasons to connect machines, aside the tax credit
written August 17 2022
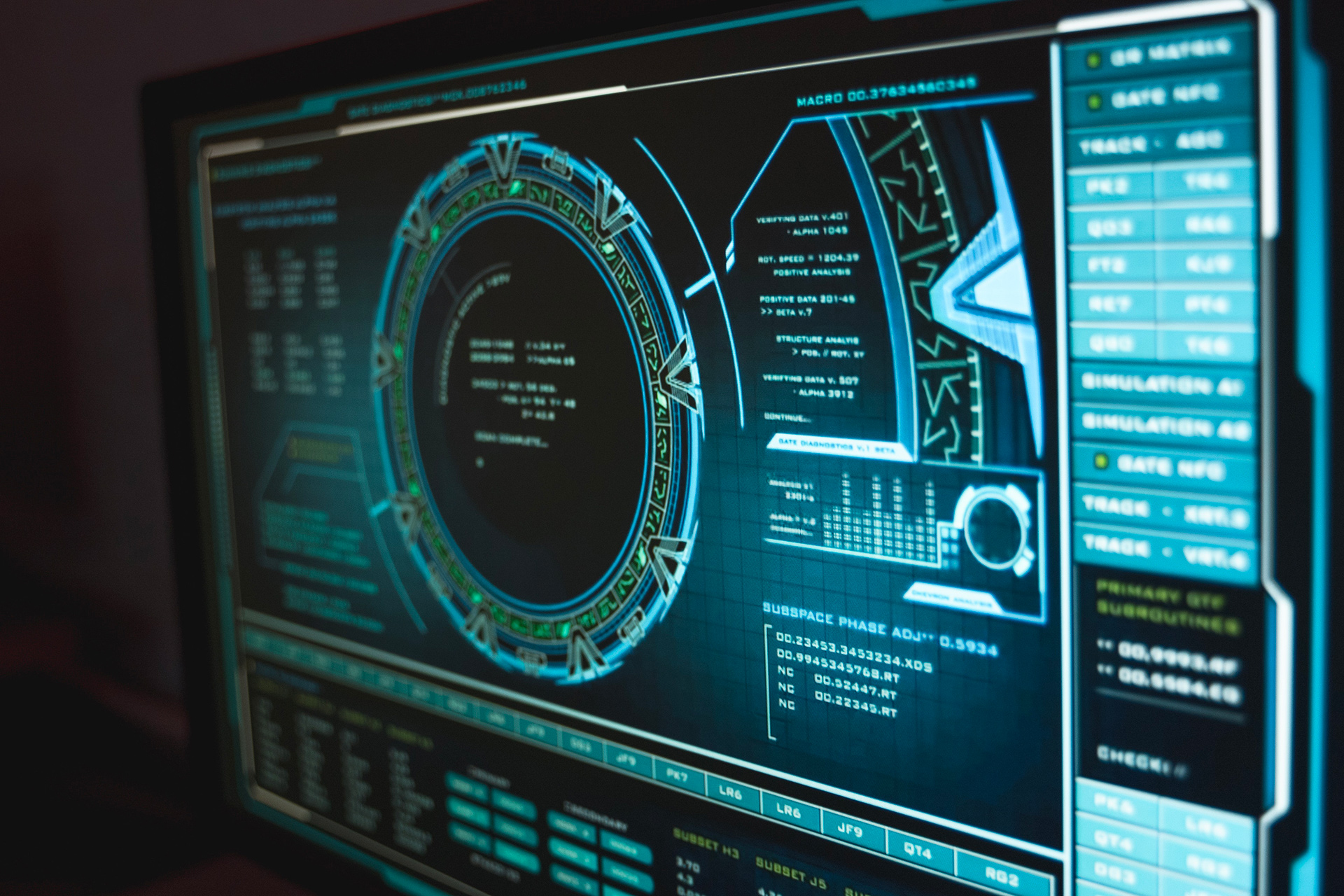
The tax credit is obviously the main reason why italian companies are looking forward to the connection of their machine to the company management system.
We would like to remind that, although a direct saving in terms of money, it is a very important and direct benefit. The right connection and application of industry 4.0 protocols brings significant advantages to the company.
Here you can see some examples.
1. Implementation of an up-to-date network infrastructure
Industry 4.0 forces companies to fix their corporate LAN. It may seem trivial, but improving the internet connection with a better and faster one allows company to save a few tenths of a second for each click on the operations done on the web. Try to multiply the clicks made every day by all the operators of the company for every working day.
The company LAN must be stable and secure, must allow a remote assistance. Also, the PCs in the company that run an old operating systems (for example Windows XP) must be dismantled, because they may lead to security breaches. This is the first step towards the digitalization of the company.
Anyway, staff also need to become familiar with internet protocols, remote assistance and a range of modern procedures that could make them more efficient.
2. Adoption of a management system
There are still many companies in Italy and Europe which do not use a production MIS.
The introduction of a system like this also forces small companies to digitize their workflow, with less paper usage and waste of manpower for information reporting in redundant ways. Our Gerp management system allows companies to delegate complex operations to workers with less experience. The experience of the whole company is moved in the management system, which becomes the main information database of the company, where nothing must be left to “someone’s memory”.
3. Data collection
An Industry 4.0 software allows you to collect a significant amount of data from your machines and equipment. At first glance they may seem useless data, but over the years they can represent a tiny gold mine. Collected data can be used to measure the efficiency of the machinery over time, provide real and non-hypothetical statistical data (speed, consumption) which could be different from those included in technical data sheets or sales brochures.
These data could become essential in the future, when a machine needs to be replaced or updated and it is necessary to compare its historical use. Important decisions regarding the purchase of very expensive machines cannot be left to chance.
4. Reduce human intervention
Another strong feature is the decrease of manual operations for the "make-ready" process, the starting of a machine. When a company has got a “recipes” archive, is better to keep it in a [production manager]. Those recipes are directly linked to orders, so the operator does not have to manually report the setup data of a machine for a particular job or commission.
If a customer wants a batch of 1000 pieces per package unit, the operator doesn’t have to type 1000 on the machine panel, but he can obtain this data from the management system which has received the information directly from the customer through an e-commerce system.
Minimal human intervention. The data “1000” within the business flow is not “typed” anymore by anyone.
5. Real time update for the warehouse
This point is a combination of the above ones.
The collected data, if properly used and linked to the management system, may be used to download raw materials in real time, without human intervention. A predisposed machine communicates the usage data linked to the codes of the involved raw materials, and them are downloaded from the warehouse in real time. Nobody types anything on any terminal or keyboard. The warehouse is updated with a "reliable" data and the sales department knows when a stock shortage occurs to proceed with order from the supplier.